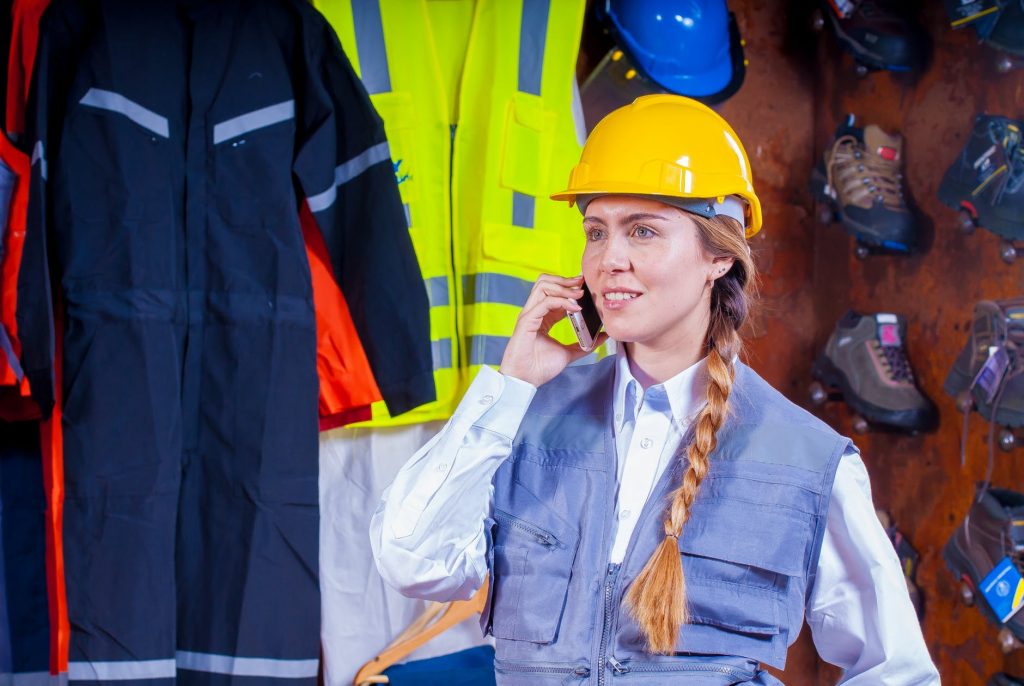
When people suffer injuries at work, the cost is far-reaching and multi-faceted. There is the injury itself, the time away from work, potential claims, and even more things to consider that will cost your business money. The monetary cost of the workplace is notably high too. In 2014 and 2015, the cost reached £4.8 billion in the UK, with £2.8 billion of that amount billed to employers. This cost doesn’t include potential claims through an accident at work solicitors. To avoid accidents as much as possible, workplace safety is key.
Here are some ways you can improve the workplace safety of your employees working in high-risk industries.
Protective Equipment
Workplace injuries are most common in the construction industry. The sector suffered 30 deaths in 2016/17. Closely followed by agriculture (27 deaths) and the manufacturing industry (19 deaths). These industries in particular often require certain safety equipment to abide by health and safety regulations such as wearing the equipment could separate your employees from a near-death experience and a non-fatal injury.
One common example of basic protective equipment in the industry is a hard helmet. If your staff fail to wear the required hard hat, any of those injuries could be a direct cause of not wearing the correct safety equipment. Protective glasses should also be worn by employees that are exposed to debris, dust and bright lights that could damage their sight.
Safety equipment extend further than just the head, of course. Other protective clothing that can be compulsory within working environments like construction and manufacturing include steel toe cap boots, hi-vis clothing, safety gloves and noise cancelling headphones. Implementing a work policy that says your staff are required to wear safety clothing and equipment is the first step to preventing workplace injuries that could lead to fatal deaths or long-term work absences, which cost your company money.
Workplace Safety Staff Training
For many industries, staff training is important to ensure all employees know how to approach their working environment. Every employee should be briefed on the safest fire exits around the premises, as well as what the procedure is in case of an emergency. In fact, many premises are permitted to carry out practice fire drills to ensure all members of staff are aware of the routine.
There’s more to consider than just fire safety measures though. In the manufacturing industry, which is the third most dangerous environment for fatal injuries in the workplace, some job roles require particular training and qualifications to use machinery. Where hazardous or dangerous machinery is involved, staff must be trained on how to use it, and must use the correct safety equipment and clothing at all times. 152,000 of the 621,000 non-fatal injuries in 2015/16 led to over 7 days of work absence
Providing your staff with the appropriate training could save you a big cost seen through a loss of working hours due to workplace injuries. You can start with osha 10 hour training, provided by 360Training.
Some processes require employees to be certified. For example, in the construction industry, any employee who will be navigating a crane will require a Construction Plant Competency Scheme (CPCS) license.
Workplace Safety Regulations
Stay up to date with safety regulation in order to protect your staff and your firm. One of the main causes of non-fatal injuries is slipping and tripping which was nineteen percent of the 621,000 workplace injury victims in 2015/16. The main causes of slips, trips and falls in the workplace are uneven floor surfaces, unsuitable floor coverings, wet floors, changes in levels, trailing cables and poor lighting. All of which can be prevented or marked out safely if the proper regulations are followed.
Legally, businesses must follow The Workplace (Health, Safety and Welfare) 1992 Regulations, which stipulates that employers must ensure that floor spaces are in good condition and free from obstructions. The Health and Safety (Safety Signs and Signals) 1996 Regulations legally require businesses to provide and display the appropriate safety signs when there is a potential risk whether that is a wet floor sign, or signs indicating loose cables or exposed electric cables.
Finally, specific industries will often have their own set of additional workplace safety measures expected of them. f